Reviving centennial marble floors in a historic Grand Rapids landmark lobby.
In addition to contract janitorial, UCS is a trusted contractor for restorative services including natural stone restoration. A historic lobby in Grand Rapids underwent a major renovation, and during carpet removal, iconic marble stone floors were discovered that had been covered with carpet and layers of adhesive for decades. UCS removed the carpet adhesive and restored the floors to their original shine.
Grand Rapids
500 Square Feet
4 Specialty Cleaners
1 Supervisor
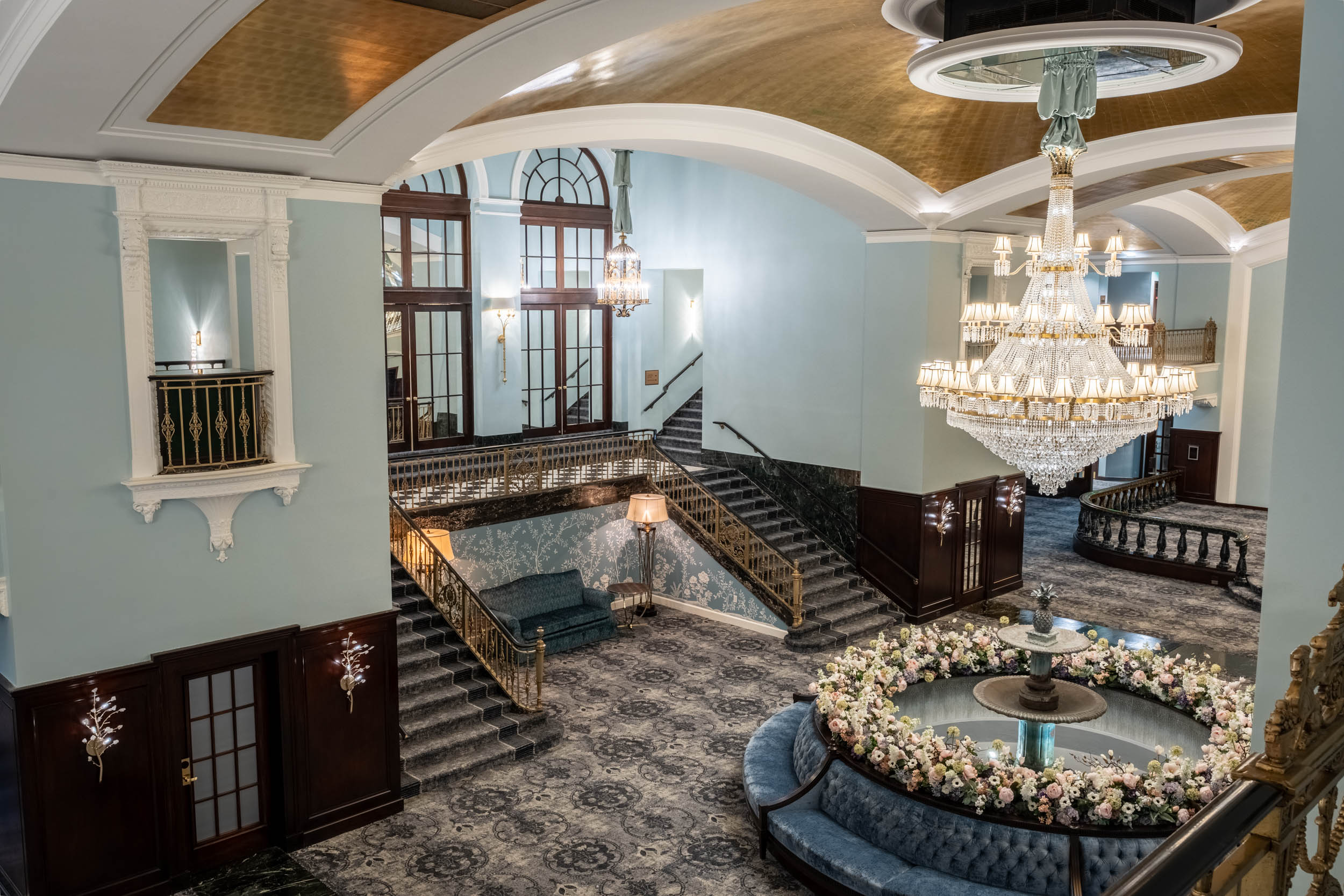
After decades of carpet covering, manual removal of carpet adhesive was required to not damage the stone surface. Once adhesive removal is completed, stone scouring would need to be removed, then the surface would require cleaning and polishing until original presentation is restored.
Stone restoration often includes lippage removal, leveling, honing, etch removal, diamond polishing, and applying protectors such as densifiers, impregnators, color enhances, and various sealers to various stone types. We have successfully restored and frequently maintain terrazzo, marble, granite, limestone, concrete, slate, sandstone, and travertine surfaces, and were eager to transform this surface back to it's original beauty.
Iconic, historic lobby, seeing a large volume of foot traffic from guests and tourists daily.
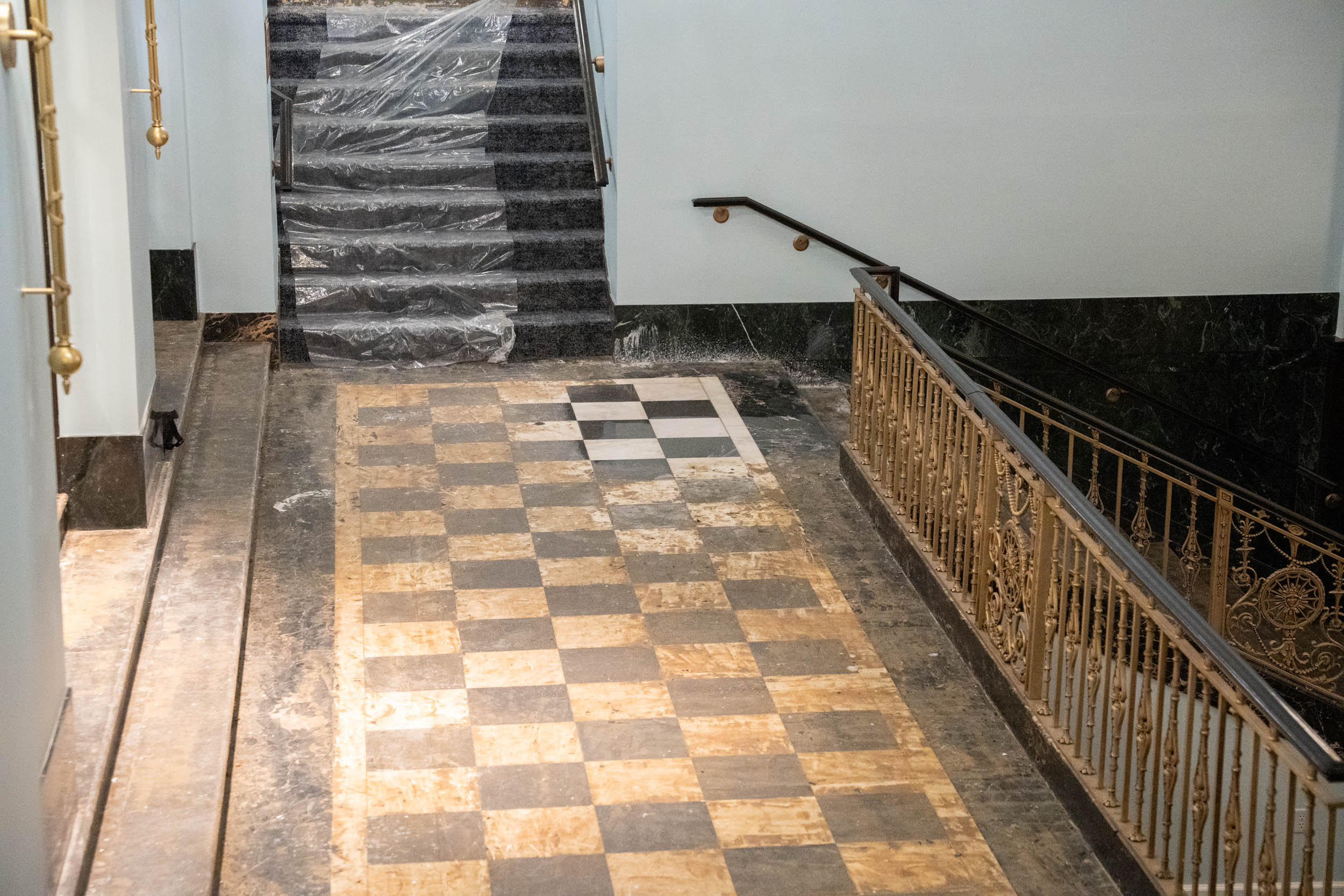
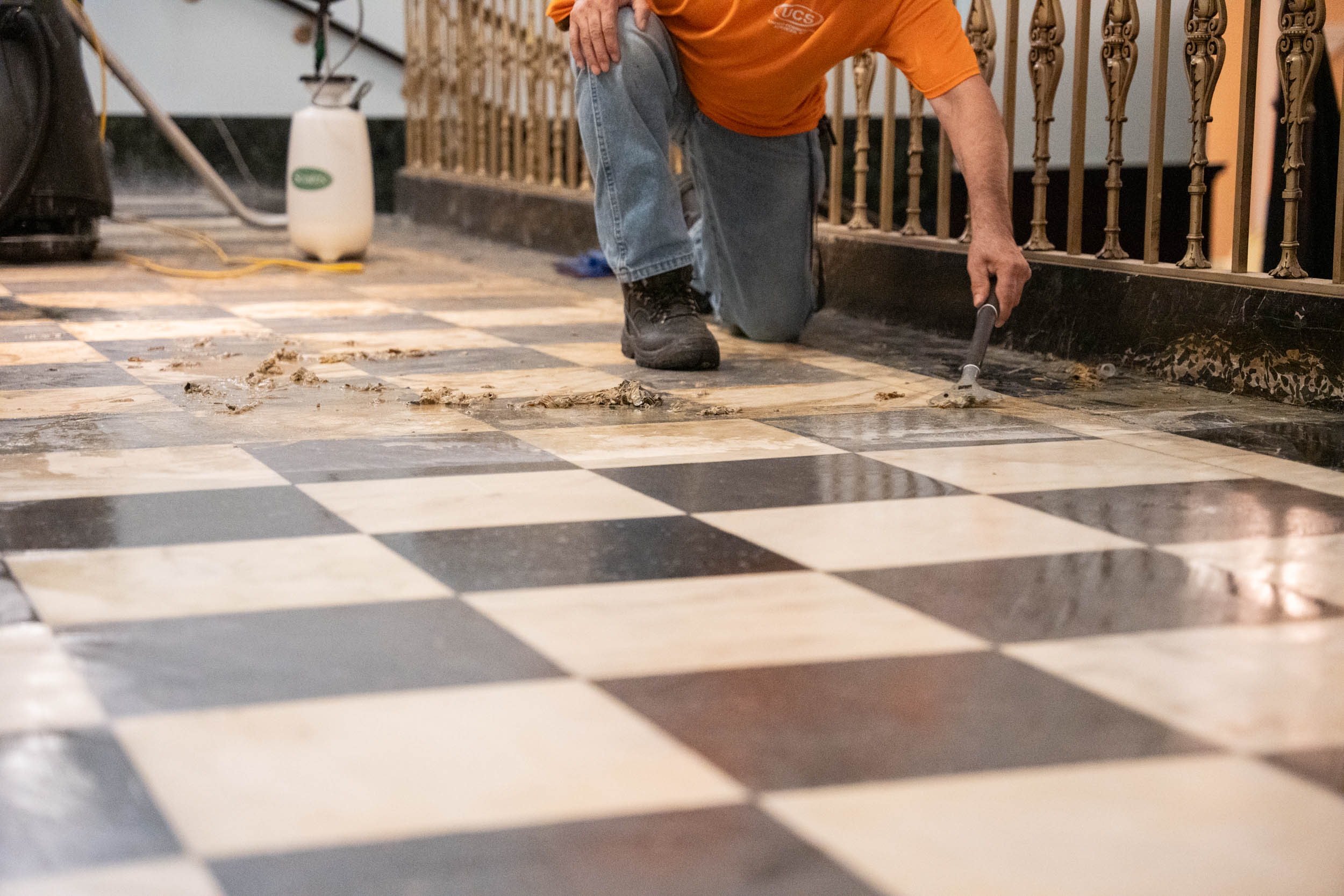
Restoration
Restoration began by removing multiple layers of carpet adhesive in a small section to expose the original stone floor, properly evaluate its condition, then determine the best process to restore it. We then cut, honed, and polished the section to prove-out our conceptual process and offer the customer options with a visual representation. Once approved, we removed the remaining adhesive with natural solvents and hand tools only, to avoid further damage to the stone.
With the adhesive removed in its entirety, additional challenges were identified which would require additional processes. At some point in the building's history, a scarifier with metal blades or discs was used on the stone to improve carpet adhesion. This scoring left very large circular scratch patterns that covered 90% of the floor, many as deep as 1/8”. Removing these scratches and other associated imperfections required the floor to be cut and leveled prior to honing and polishing the full area.
Grinding & Honing
Since the checkered stone floor was made by interlacing marble and granite, marble being significantly softer than granite, a specialized grinding approach was required. We tested a multitude of hybrid and transitional resin-based diamond discs to correct the damage, then utilized the most optimal combination on the unique floor, with very precise, fine grinding in the final stages. Once completed, the floor was level and smooth enough to begin the honing and polishing process. We performed a 3-step honing and polishing process utilizing 3M’s Diamond Trizact system. This removed the remainder of the fine surface scratches and produced a gorgeous satin sheen.
Final Polishing
Polished floors are measured by the Distinction of Image (DOI). This refers to how clearly defined an image is that is reflecting off the surface. Finely polished stone like marble and granite will have more of a glass appearance vs a floor coating that is blurred and has a plastic / acrylic reflection. This floor deserved a high DOI glass appearance, as it would have featured when it was new. We transitioned from the low-speed weighted stone floor machine and resin-based diamond discs to a lightweight high-speed burnishing / polishing machine, paired with a 3000 grit flexible diamond pad. This produced a significantly higher DOI for a reflective finish.
The final restoration stage was to protect the newly restored floor, as most natural stone is highly porous and very susceptible to staining, soil loading, and etching if left unprotected. We applied a single coat of 3M Stone Floor Protector; a densifier, gloss enhancer, and stain protector. Once the protector cured, we polished the floor again using the high speed burnisher and the 3000 grit diamond pad. As a final safeguard to ensure the surface finish was absolutely perfect, we applied an additional coat of 3M Stone Floor Protector and high speed polished the floor one last time.
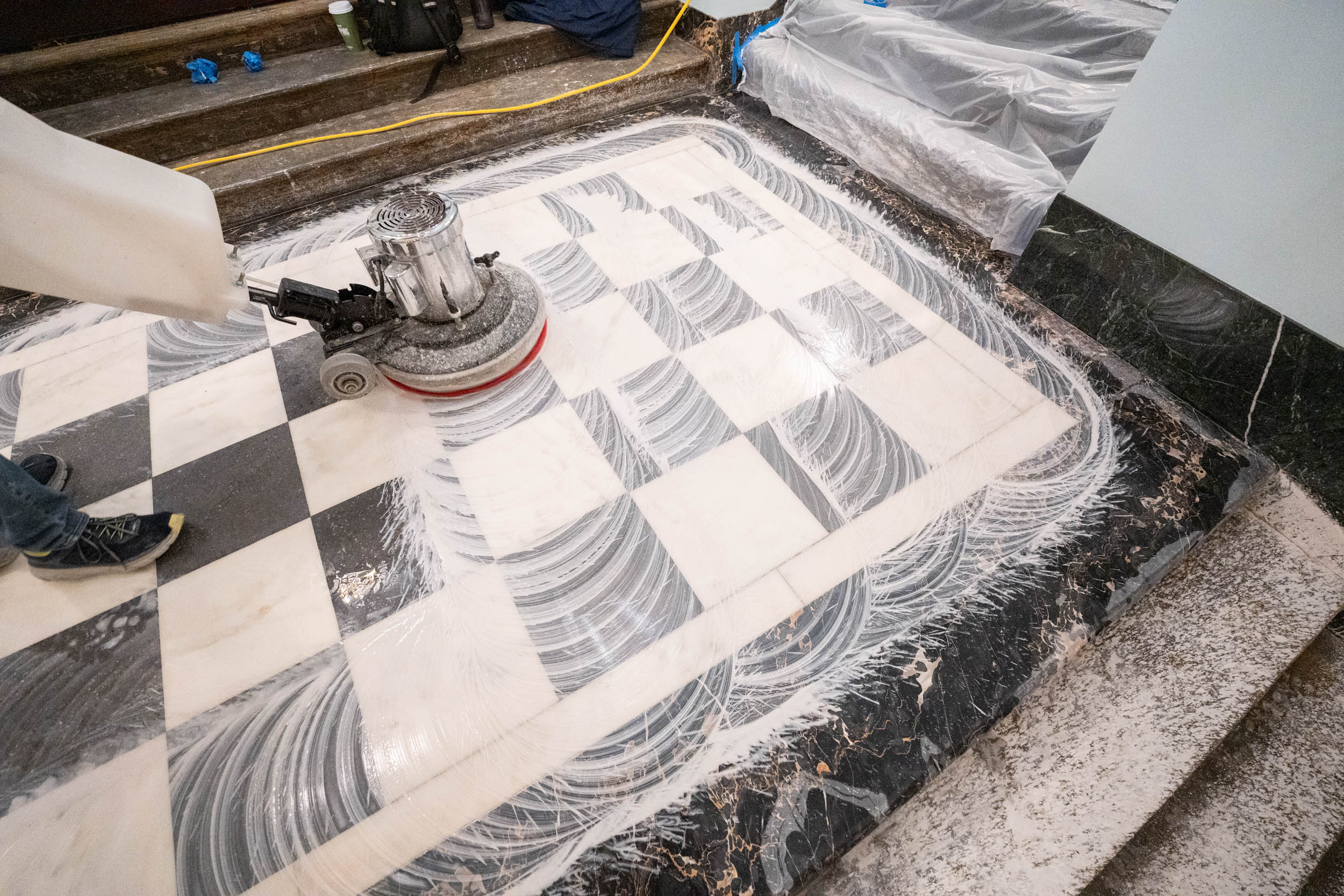
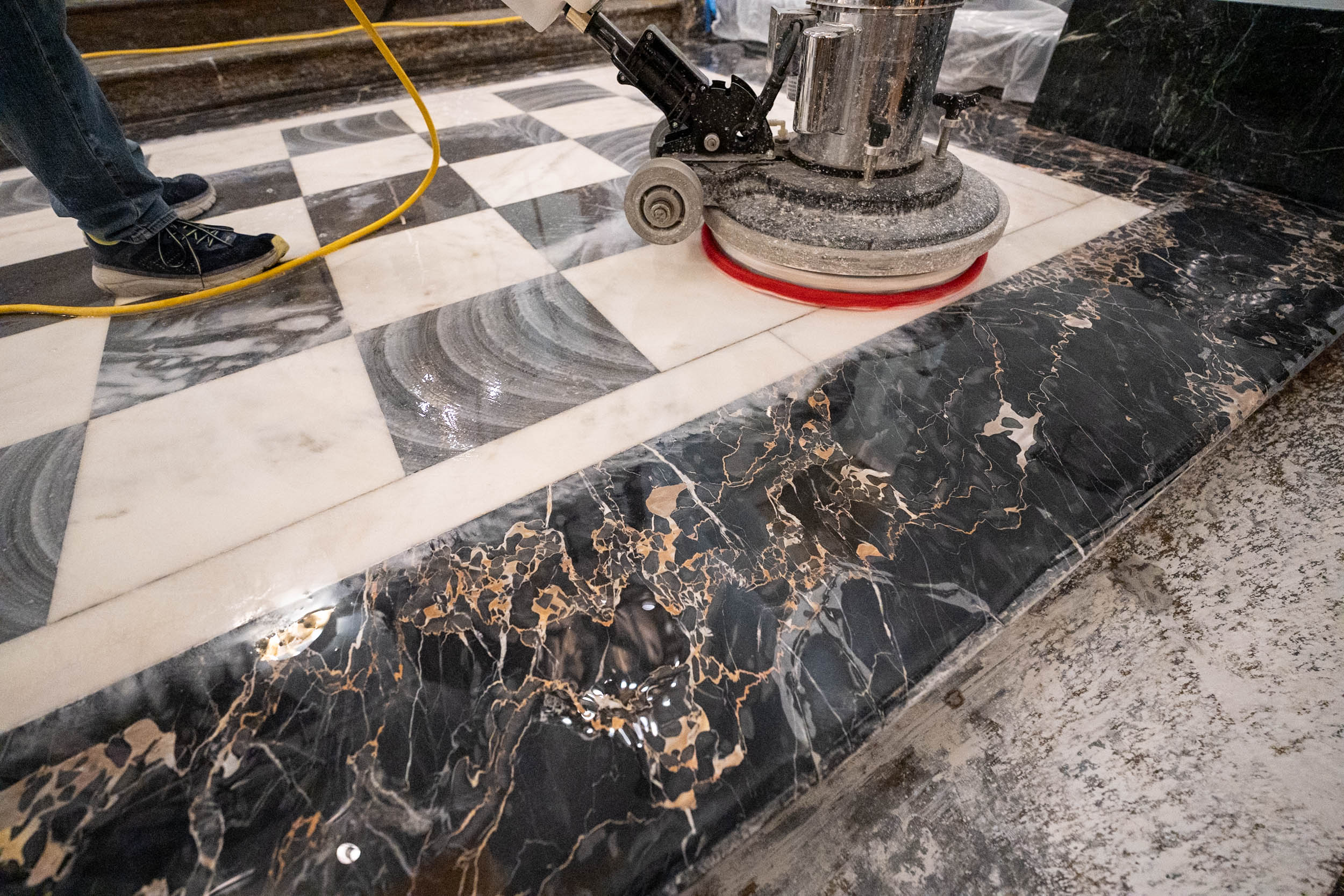
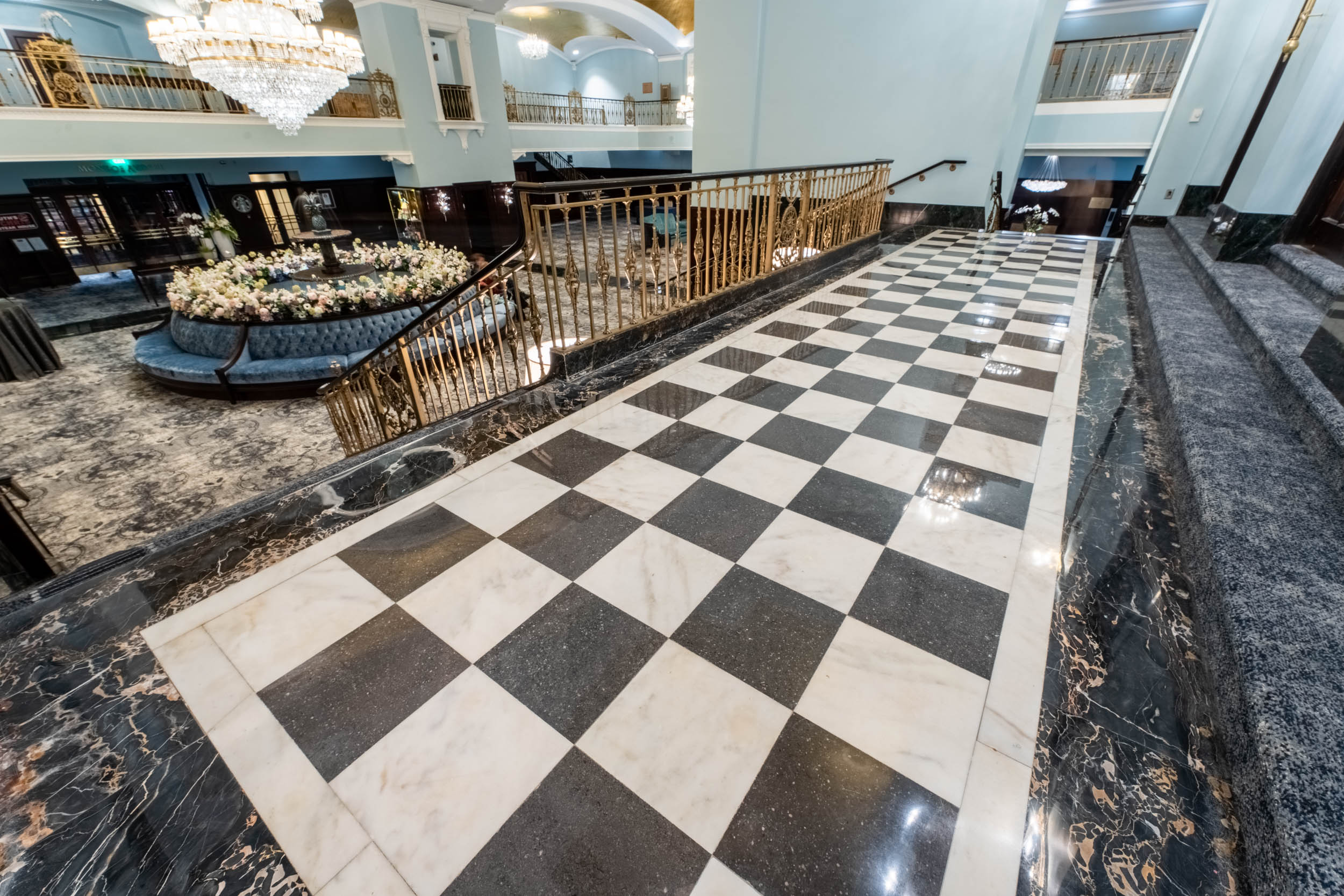